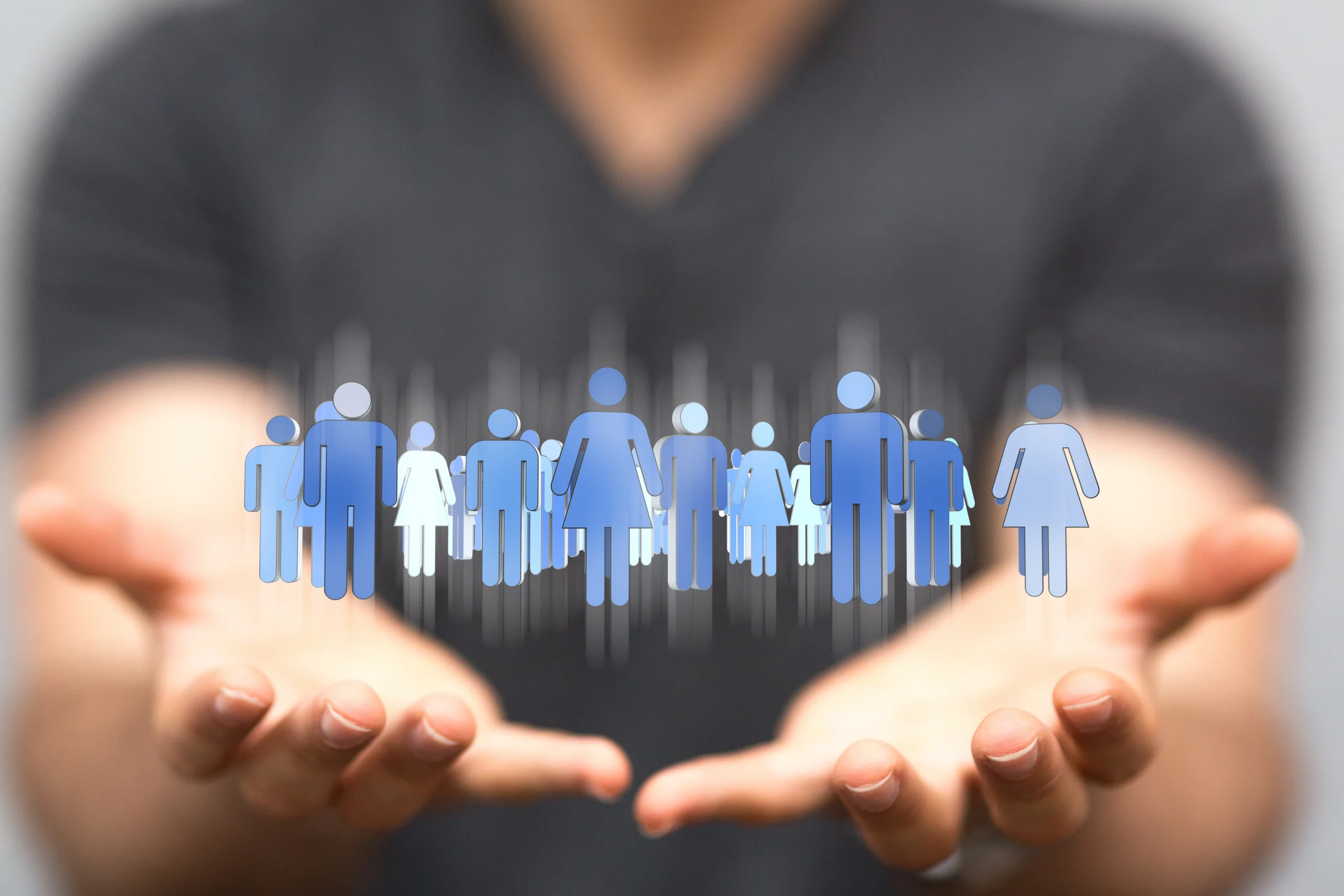
SBy Torsten Kruse, founder and president, Kruse Analysis, Inc. and Kruse Training, Inc.
In an era defined by rapid technological advancements and evolving workplace dynamics, the success of any organization hinges on its ability to strategically manage its workforce.
The Attract – Train – Retain (ATR) Framework is a strategic approach to workforce management that underscores the interconnected nature of attracting top talent, developing their skills and expertise and retaining them for the long haul. Each element feeds into the others, creating a harmonious strategy aimed at achieving organizational excellence.
Attract: Drawing in Top Talent
The first component of the ATR Framework, “Attract,” is centered on the art of drawing top-tier talent into the organization. In a world where competition for talent is tight, organizations must employ innovative strategies to set themselves apart and appeal to the brightest minds.
This begins with modernizing perceptions of the industry and showcasing its innovative facets, automated processes and promising career growth opportunities.
Key Strategies for Attracting Top Talent
- Modernize Perception: The manufacturing industry often suffers from outdated stereotypes. To attract talent, it’s vital to address these misconceptions by highlighting the industry’s cutting-edge technologies and career prospects.
- Technology Showcases: Organize open houses or events that showcase cutting-edge technologies. Robotics and computer simulation technology can ignite excitement and interest among prospective employees.
- Educational Partnerships: Collaborate with schools, colleges and vocational programs to help demonstrate the practical applications of manufacturing and injection molding. Encouraging students and parents to consider careers in these fields.
- Competitive Compensation: Emphasize the earning potential and job stability within the manufacturing sector to pique the interest of potential employees.
Train: Developing Skills and Expertise
“Train,” the second pillar of the ATR Framework, focuses on nurturing the skills and expertise of the workforce. In today’s rapidly evolving landscape, employees must continually develop and adapt to stay relevant. Effective training programs are essential to equip employees with the knowledge and skills needed to excel in their roles.
Key Strategies for Developing Skills and Expertise
- Continuous Learning: Cultivate a culture of continuous learning within the organization. Provide employees with access to relevant training and development resources to keep their skills up to date.
- Personalized Development Plans: Recognize that each employee has unique strengths and weaknesses. Tailor development plans to individual needs and career goals, fostering a sense of investment in their growth.
- Focused/Micro-Learning: Implement clear and concise learning methods that promote results. Short, targeted learning modules can be particularly effective in enhancing specific skills.
- Reinforce Theoretical Learning: Combine theoretical learning with real-world examples, virtual reality lab lessons and hands-on experiences. This practical approach enhances understanding and retention of complex materials.
Retain: Keeping Your Employees
The final element, “Retain,” underscores the critical importance of retaining valuable talent once they are part of the organization. High employee turnover can be detrimental to productivity and organizational stability. Therefore, creating an environment that fosters retention is paramount.
Key Strategies for Retaining Employees
- Enhanced Collaboration: Crosstraining employees fosters a collaborative work environment. It also reduces the risk of operational disruptions when employees leave the company or new team members are onboarded, as multiple employees can perform essential tasks.
- Career Pathways: Establish clear and structured career paths within the injection molding industry. Show new employees how they can start at entry-level positions and progress to more skilled roles with increasing responsibilities and rewards. This provides a sense of direction and purpose.
- Workplace Culture: Cultivate a positive and inclusive work environment. Highlight the benefits of teamwork, problem-solving and the sense of accomplishment that comes with creating tangible products. A strong workplace culture can contribute significantly to employee satisfaction and retention.
In conclusion, this framework – Attract, Train and Retain – serves as a holistic strategy for strategic workforce management. In an ever-changing business landscape, attracting top talent, continuously developing their skills and retaining them are essential for organizational success.
By interweaving these elements and implementing the key strategies outlined in each category, organizations can build a workforce that not only excels in the present but also adapts and thrives in the future. Embracing these elements is a proactive step towards ensuring sustained excellence and competitiveness in the modern business world.
Trends in Training for Mold Builders
In the ever-evolving landscape of mold design and manufacturing, staying abreast of the latest trends and technologies is crucial for mold builders in 2024. We had the opportunity to explore these issues during the recent TechXellence Training Summit.
Here are some insights shared by industry experts:
What are the trends in training programs and technologies that mold builders should look for in 2024?
In 2024, the mold building industry is witnessing a shift towards a more inclusive training approach that encompasses all facets of the mold design process. It’s becoming increasingly vital for mold designers to possess knowledge not only in mold construction but also in plastics, part design and processing. This “Circle of Knowledge” holistic approach allows designers to optimize their creations before the mold building process begins.
Furthermore, the use of Computer-Aided Engineering (CAE) simulations is gaining prominence. These simulations go beyond analyzing polymer flow and warpage to ensure part quality. They also encompass Computational Fluid Dynamics (CFD) simulations and mold thermal analysis to guarantee well-designed water circuits and uniform cooling, ensuring the mold’s optimal performance. Embracing modern design technologies is essential in ensuring quality and staying competitive.
What questions should mold companies ask before deciding on and starting a new training program(s)?
Before embarking on a new training program, mold companies should consider several essential questions. First and foremost, they should assess the benefits the program will bring to the organization. Beyond this, it’s crucial to determine if all employees require this training.
In today’s fast-paced industry, continuous learning is key, making training a cultural component rather than a one-time event. By ensuring that all employees are re-skilled and updated on new design and mold-building technologies, a company can create a versatile pool of talent that can be flexibly deployed within the organization. This not only enhances the company’s adaptability but also fosters a more dynamic work culture, encouraging cross-departmental collaboration, team spirit and resilience in case of personnel changes.
What are three ways mold companies can improve their training practices and methods?
Mold companies can enhance their training practices and methods by adopting the following strategies:
- Accessible Training Systems: Implement a training system that can be accessed anytime, anywhere and on any device. Accessibility to information is crucial in a rapidly evolving and fast-paced industry. Providing employees with immediate access to focused learning materials, including micro-lessons, enables efficient training and optimizes the balance between learning and work responsibilities.
- Continuous Learning Culture: Promote a culture of continuous learning within the organization. Training should not be viewed as a one-time event but rather as an ongoing commitment to staying ahead of industry developments. Encourage employees to seek out new knowledge and skills, fostering a workplace culture that values growth and adaptability.
- Crosstraining: Encourage crosstraining among employees. This not only broadens individual skill sets but also creates a workforce that can seamlessly transition between roles, departments, and projects. Crosstraining enhances teamwork, builds stronger relationships among employees and ensures that the organization remains resilient in the face of challenges.
Incorporating these strategies into their training practices will empower mold companies to thrive in an industry marked by continuous innovation and change.
Torsten Kruse is the founder and president of Kruse Analysis, Kruse Training and the highly anticipated VR innovation, Molding Expert. With an illustrious career spanning nearly three decades, Kruse has played a pivotal role in advancing injection molding, offering cutting-edge CAE simulation services, software applications and premier online training for design and process engineers. Before starting his own companies, Kruse had a successful seven-year career with Arburg, Inc., working on various molding applications and developing and delivering training programs in Germany and the US.
The Kruse Training platform offers invaluable learning opportunities tailored to novices entering the field and professionals seeking to enrich their expertise. Kruse is dedicated to imparting intricate nuances of injection molding to aspiring part designers, mold designers and process engineers.
More information: www.krusetraining.com