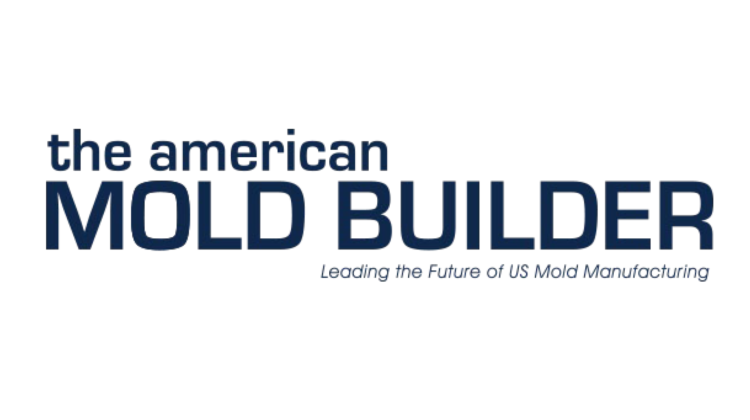
An interview with Jim Bott, business development manager of mobility/automotive/heavy truck, INCOE
Hot runner technology has been around for decades. However, it’s piquing plastics processors’ interest, and sales have been increasing over the past 10 years. The technology has made encouraging advancements and manufacturers are capitalizing on its benefits. Known for efficiently and precisely delivering molten plastics to the mold cavity, hot runners offer a number of advantages, including design flexibility with no limitations, quicker production cycles, waste reduction and improved part quality output.
The American Mold Builder reached out to Jim Bott, business development manager of mobility/automotive/heavy truck at INCOE and an industry veteran, for his perspective on hot runner technology.
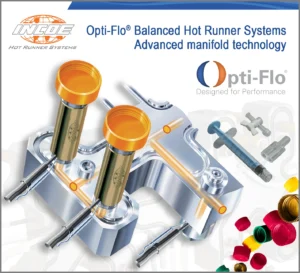
Hot Runner technology is utilized in markets including automotive, medical, packaging, electronics and more. Where is the market growth, and how are hot runners enabling those applications?
Yes, certainly “more” markets (in alphabetical order) such as appliance, caps/closures, cosmetics, defense, lawn and garden and recreation can be added to the question.
Each one of these markets then is subdivided into numerous categories. Not taking the easy way out, the belief is market growth opportunity hits “across the board” for the various applications. The exception may be non-critical, single-use parts where recycling is not commonly practiced. Organizations, namely PLASTICS, are lobbying and educating both with the government and the public regarding proper human care of recycling as the solution rather than banning certain single-use plastic products. This important message, turned into practice, will delete the noted listed exception to market growth.
Hot runner technology, in many cases, is the only approach to meet the final product demand(s). These needs include, but are not exclusive to, part quality, weight reduction, production volume and material scrap reduction.
Where does hot runner technology play a part in sustainability?
Interesting references to “hot topics” and “hot runner!” Hot runner melt delivery technology always has contributed to the reduction of CO₂ emissions. However, rarely was it or was it not mentioned just five years ago. Now, it has become a topic of higher recognition. Some global governments “reward” the pursuit of reducing carbon emissions – as an example, giving grants to those that demonstrate investments in technology that lowers CO₂ emissions over the currently used technology(ies).
Other governments “penalize” those that do not provide proof of CO₂ reduction. As an example, the governments may impose higher taxes for those businesses that do not demonstrate the implementation of emission-reduction technology. Hot runner technology when directly comparing gating on the part to cold runner technology – and, more so, parts that must be processed with zero regrind – reduce CO₂ emissions.
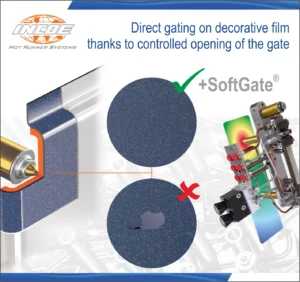
INCOE’s most impactful CO₂ reduction hot runner technology is Opti-Flo® – a Beaumont Technologies implemented science, that often reduces part scrap rate and increases productivity when compared to using conventional hot runner melt delivery technology. This is accomplished by managing the melt to ensure the homogeneous distribution of plastic laminates, both part to part and within the part. Using the before and after, molded parts per hour results then can be entered into a provided presentation to get quantified data on the CO₂ emissions reductions. The results now are documentation of the advancement of sustainability.
Further, energy savings are realized with the use of thermal blankets on the injection molding machine barrel and hot runner system.
What sensors or technology can be added to hot runners to help track cycle counts, anticipate maintenance needs and Increase Production efficiencies?
Since the markets and sub-categories of each market are broad, there must be a vast offering of hot runner auxiliary technologies to enhance profitability. Not all these technologies necessarily are the lowest price/performance ratio for certain applications. Bott’s slang is, “There are different horses for different courses.” Some run best in dry course conditions, whereas others outperform the field in muddy conditions. Selecting the proper “horse” for the application is critically important.
First, the design and construction of hot runner heaters, thermocouples, manifolds and nozzles now optimize insulation/isolation. In addition, PIDD temperature controllers and valve-gate sequence controllers, combined with (and/or) FEA thermal, filling and warp analysis technologies, have advanced over the years.
Second, there exists hot runner melt management technologies for thermal-gated and valve-gated applications. The latter, valve-gate, can be live-monitored with valve gate sequence controller technology. Pressure transducers can be added to the injection molding machine and/or the mold cavity(ies). Thermocouples can be added to the mold cavity(ies). These sensors will provide live (every shot) data that is graphed – pressure vs. time – on the valve gate sequencer monitor. INCOE uses RJG architecture and sensors.
If required (i.e., parts that require multiple valve-gated nozzles to properly fill the part), valve-gate pin retraction speed technology can be included with the hot runner to improve part aesthetics and reduce maximum injection pressures. This improves the process window while reducing scrap.
Progressive Components has live monitoring cycle counter technology that is added to the mold parting line. Software that collects and displays data is very useful for the molder. Hot runner parameter data can be entered, such as preventive maintenance when a certain number of cycles is reached.
Lastly, sensors can be used to collect data and share that data with other equipment within a molding cell for monitoring or to trigger an action. Additional sensors for measuring various parameters can be installed on the hot runner system or on the corresponding supply lines. Examples are plastic leakage, water temperature, valve gate media monitoring and/or valve gate function monitoring. This sensor data is connected to a data logger with output and control software to display the measured data, so the process can be monitored and/or acted on.
In conclusion, Bott shared, “The auxiliaries add cost to a very price-competitive mold-building market. Everybody wants technology – until the price tag is seen. But the addition of the technology only is profitable to the molder and/or OEM when properly selected.”
Over the past 38 years, Jim Bott has been employed at INCOE Corporation, a world-class global supplier of hot runner systems as the business development manager of automotive and heavy truck for North America. Bott has held past positions as draftsman, designer, checker, applications engineer, engineering manager and North America sales manager.
More information: www.incoe.com