by Ryan Weister, application engineer
UNISIG
A mold manufacturing process concept is allowing mold shops to increase productivity and optimize profitability. The catalyst for these process changes is the combination of sophisticated multi-axis CNC machining center capabilities with those of a high-performance deep hole drilling machine.
These multi-axis, combined machining/deep hole drilling machines not only offer easy compound angle machining and drilling due to standard 4th and 5th positioning axes (B-axis rotary table and A-axis tilting headstock), but are a key strategy for manufacturing molds as efficiently as possible. With such technology, mold shops can perform the machining center operations and the deep hole drilling operations all on the same machine tool.
This means mold blocks only move to one machine, as opposed to back and forth between a separate machining center and gundrill machine, as is the case with traditional mold processing operations. Furthermore, previously time-consuming setups are greatly reduced or even eliminated to complete the processes required after rough-sawing a mold and prior to high-speed finishing it.
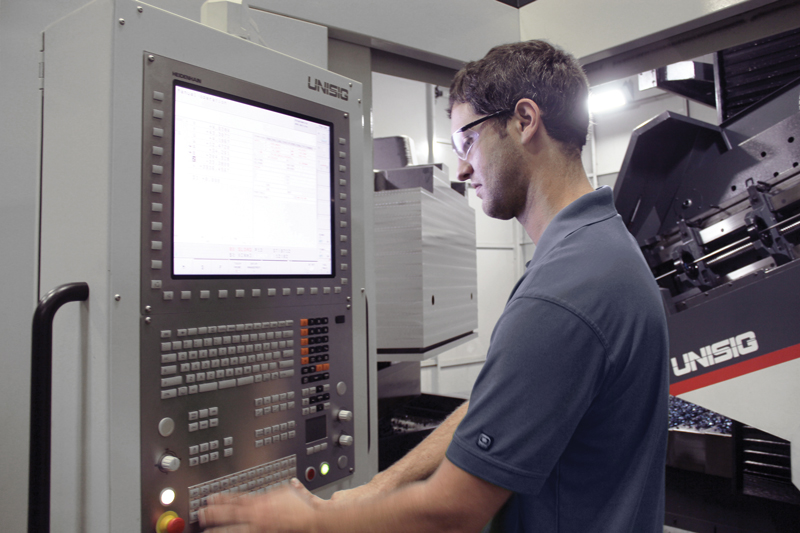
Understanding capabilities
These machines are essentially a 5-axis CNC machining center with extreme reach capability, table weight capacity, high accuracy and optimal rigidity. Some machines even have an independent machining spindle and deep hole drilling spindle to allow optimum cycle times, since operator intervention is not required for changeovers between machining and drilling.
To optimize productivity, operators can program the machine to counter bore various holes with a 50-taper machining spindle, for instance, retract the machining spindle quill, and deep hole drill the mold block’s water lines via the independent drilling headstock. The machine then can automatically change out the tool from an endmill to a thread mill and add NPT tapped holes to those water line ends. All of these steps – typically done on multiple machines – can be completed unattended in the machining system. Such systems even allow for process quality checks via touch probes available for the machining spindle, along with a laser tool pre-setter.
A high-performance combination deep hole drilling/milling machine also should provide the technical advantages of both gundrilling and BTA drilling. Most machines only offer gundrilling. Although some machines can utilize higher feed rates with new technology such as indexable gundrills, the BTA system allows higher penetration rates compared to traditional gundrills or indexable gundrills. BTA tools work best in hole diameters greater than 0.500″ (12mm). Deep holes less than 0.500″ (12mm) in diameter still utilize traditional brazed tip gundrills.
Combination deep hole drilling/milling machine tool builders must understand the advantages and applications for both types of deep hole drilling processes used during mold manufacturing. Those that do engineer machines with not only independent spindles, but with a drilling headstock that can perform both gundrilling and BTA drilling to allow the highest productivity. Such machines also allow mold shops to use the necessary deep hole drilling tools (conventional gundrills, indexable gundrills, brazed BTA heads, indexable BTA heads and spade BTA heads).
Effortless changeover also is critical for optimum efficiency. Quick adapters can provide changeover from gundrilling to BTA in less than 10 minutes. The feed rates possible with BTA tools are five to seven times faster than traditional gundrills. Higher coolant flow, more efficient chip evacuation through the BTA tool head and larger drill tube bore, and a more rigid drill shank (the BTA drill tube) all work together for higher BTA drilling process penetration rates. For optimized cycle times, not only does the optimal tooling need to be used for the application, but the machine tool must have the capability to effectively run the tools.
Coolant control is critical in deep hole drilling and milling operations. Those machines that provide the most accurate coolant flow to the tool are ones that incorporate advanced high-pressure coolant systems with fixed displacement pumps driven by high-performance motors with variable frequency drives. With such systems, the flow rate can be variably programmed in the machine CNC and set in a tool table for the specific tool in use. This allows tools from as small as 0.125″ (3mm) in diameter up to 2″ (50mm) in diameter to run automatically on the same machine.
Mold shops can effectively monitor the drilling process by monitoring the coolant pressure while providing a precise amount of known coolant flow via the fixed displacement pumps during every drilling cycle. Analog pressure transducers provide closed-loop feedback to the machine control to monitor programmable pressure limits for each tool in a shop’s tool library. The machine will cycle-interrupt to prevent tool or workpiece damage before the tool breaks.
Drilling thrust and torque also are monitored, and limits can be programmed for each tool as well. Advanced dedicated coolant systems also are ported to the machining spindle so that shops can apply high-pressure coolant to any machining spindle tools being run. Just as the control can store drilling tool parameters, the tool parameters can be set and monitored for each milling tool.
At their mechanical cores, combination deep hole drilling/milling machines must deliver optimum rigidity. Strong machine frames; high moment load bearings on rotary axes; high weight-capacity table designs, rigid linear roller guiderail axis motion driven by high-performance ballscrews coupled to intelligent servo motors, and premium transmissions driving rigid spindles must all work together for both deep hole drilling and machining tools to be pushed to their limits and with high-precision results. Machine kinematics and linear/rotary encoders (scales) on all positioning CNC axes further improve overall machine accuracy.
Production advantages
Traditionally, molds are produced in multiple manufacturing steps. Small to extremely large molds for various industries all begin as solid blocks of tool steel. Large band saws cut the blocks to remove as much material as possible, and afterwards, the blocks move to either a basic horizontal boring mill or to a large vertical-spindle roughing machine for roughing operations where the block starts to resemble a mold, as piles of large, heavy chips are removed.
Once roughed, the blocks get sent out for a stress relief process, after which they get semi-finished on a typical 4-axis CNC (X, Y, Z, and optional B-axis) machining center. Once semi-finished, the blocks move on to a gundrill machine for the time-consuming drilling of numerous deep holes, mainly for water lines in the mold. Many mold shops use common 3- or 4-axis gundrills that allow holes to be drilled at various X/Y positions and also at angles if the 4th axis (B-axis rotary table) is available on the gundrilling machine.
What most shops rarely use are 5-axis gundrills (X, Y, Z axes and a B-axis rotary table along with an A-axis tilting headstock.) The 5th axis working in tandem with the B axis makes it possible to do compound angle gundrilling. Most molds do require compound angle deep hole drilling, since water lines must be designed to navigate their way through the complex molds to ensure proper cooling and performance. For a great many mold shops, it is this deep hole drilling process that frequently presents a bottleneck in their manufacturing process, and the problem is further magnified if the gundrill machine has a 3- or 4-axis configuration.
The time-consuming process – and ultimately costs – required to gundrill on a 3-axis machine can have devastating effects on a shop’s profit potential. To drill any hole on a 3-axis machine, the mold block has to be moved and set up so the spindle is aligned with the proper drilling plane. If compound angles are required, fixture setup poses further difficulties and consumes even more time.
Special fixtures or sine plates are required to drill at compound angles, which again equates to additional setup time. Plus, highly skilled experienced operators are needed for these difficult mold setups on 3- or 4-axis machines, and that translates into higher costs per hour.
After drilling, mold blocks must often return to a machining center that generates additional features, such as counter-bored holes, pockets, threads on the water line holes that were just gundrilled, tapped holes and more. In some instances, the mold may travel back and forth between machining center and gundrill several times, which in turn means multiple machine setups, large mold blocks traveling around a shop more than necessary and additional manufacturing costs. Once the mold is done going back and forth between the machining center and gundrill, it most likely moves to a 5-axis CNC high-speed machining center for finish machining. To eliminate these steps, the milling accuracy of a combination deep hole drilling/milling machine must be comparable to that of a machining center.
Efficiency provides results
Manufacturing the exact same part – a mold block, for example – in less time allows more parts to be manufactured per year, which brings in more revenue per year. The costs to manufacture the mold are reduced because it takes less labor and less time to complete the job – based on all the advantages the combination milling/drilling machine offers. More parts manufactured in less time at a lower total manufacturing cost equals more profit.
Ryan Weister has been a part UNISIG’s engineering team for more than six years, working on machine tool mechanical design, project management and in his current position as an application engineer. He was raised in northern Wisconsin and graduated from the Milwaukee School of Engineering (MSOE) with a degree in Mechanical Engineering. Prior to his work at UNISIG, he ran CNC machines at a local machine shop, giving him hands-on experience to complement his engineering education.