By Liz Stevens, writer, The American Mold Builder
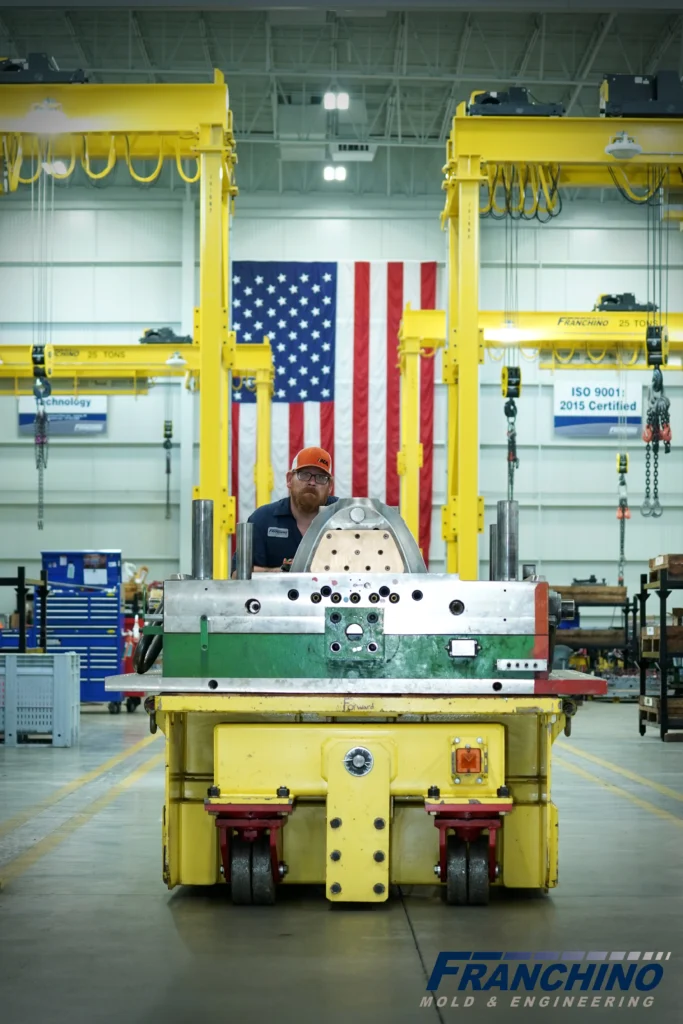
Franchino Mold & Engineering (FMEC), Lansing, Michigan, has served the mold and die industry since 1955. The company offers die cast dies, plastic injection molds, contract machining, die/mold repair and engineering services to the automotive, construction, consumer products and material handling industries. FMEC stands out, from its competition in two ways: It occupies a special niche in producing medium to large (including XXL) molds and dies, and it is a respected company operating on the cutting edge with its business philosophy and operation style, while embracing innovation and workforce development strategies. The company’s culture and its practices in employee recruitment, candidate selection, employee benefits and workforce retention stood out to The American Mold Builder, prompting a closer look. Brad Rusthoven, human resources manager, provided insight into FMEC’s best practices.
Attracting Talent
FMEC’s website, often a first impression for job seekers, reflects the company’s production standards, its perspective on technological innovation and its attitude toward its workforce. The website presents a company that works in meticulous medium- to super-sized production, employing dedicated associates who combine expert skills with state-of-the-art equipment in a modern, supportive environment. The website also is designed to make it easy for prospective employees to learn about jobs in manufacturing, see the job opportunities and apprenticeships available at FMEC, understand the company’s employee benefits and apply for a job through an online form.
FMEC clearly presents its culture on the website: “Our culture of continuous improvement, implementation of lean techniques and pushing ourselves to improve daily means that we stay on top of the latest technology, tools, techniques and quality systems.” During an employee interview, identifying job candidates who can embrace this culture and become valuable assets to the company is a two-step process. “The first step,” Rusthoven explained, “is finding the ‘right’ person. We do this by describing our core values for team members during an interview – hardworking, innovative, teamwork, integrity and trustworthy – and asking candidates to give examples of how they demonstrate each of these values. If the candidate demonstrates that he or she is the ‘right’ person, the next step is for us to find the ‘right seat’ for them from a role/responsibility standpoint.”
The seats available in today’s manufacturing are a far cry from the picture of industry roles and working conditions that have persisted from their earlier days. Presenting today’s manufacturing environment, especially in a resurging industry with an already tight workforce pool, helps FMEC recruit talent. “We have been waving the flag for manufacturing since the recession nearly 15 years ago,” Rusthoven said. “The industry we are in is no longer a dark, dingy manufacturing setting. It is a clean, well-lit, safe working environment with the highest technology and the most advanced computerized equipment on the market.”
Being a company on the cutting edge with advanced technology, tools and techniques can be an attractive environment for a job seeker. FMEC conveys this characterization as part of its culture. “This ties back to our ‘innovative’ core value,” said Rusthoven. “The company wants to be innovative and to implement technology that is advanced, flexible and automated; the majority of our equipment has been purchased in the past 10 years. From a technique standpoint, we want to define a process and follow it. However, we want our employees to be innovative as well. If they have a better way to do something, we want them to speak up so that we can evaluate new ideas and change the process, if warranted, for continuous improvement.”
FMEC’s position as a producer of super-sized dies and molds makes it stand out as a unique employer. “We let candidates know that our niche is designing and manufacturing medium to large plastic injection molds and die cast dies,” Rusthoven explained. “We show them this on the tour that we give during the interview. Some candidates are intrigued by the idea of working on big molds and dies, and others honestly are intimated by the size of the work. If they are mechanically inclined and have some foundational skills, we can train candidates who have a good attitude and work ethic and are punctual. In general, we will hire for character over skill; we can teach them what we do.”
Workforce Source: Career Centers
FMEC collaborates with two local career centers to cultivate new workforce candidates with precision machining training. The partnerships began when Rusthoven contacted the career centers. “Our relationships with both local career centers (which have specific precision machining programs) began in 2011,” he explained. “I reached out to both instructors, and they invited me over to learn about their programs and gave me tours of their facilities.”
Rusthoven’s outreach led to a spot on each of the career centers’ advisory boards and FMEC’s participation in career center events, including in-class presentations, mock interviews, resume reviews, career days, student showcases and open houses. The relationships also led to the company hosting activities at its facility – tours, job shadows and work-based learning opportunities.
“The endgame,” said Rusthoven, “is to become the ‘employer of choice’ for the precision machining programs at the local career centers. We want the instructors, counselors and work-based learning coordinators to refer their top students to us after graduation.”
Cultivating Skills In-House
FMEC offers apprenticeships and an educational benefit to attract new workers and to help retain its valuable workforce. Two tracks are available – journeyman’s card or journeyman’s card plus an associate’s degree or certificate – and it’s all on Franchino Mold & Engineering’s dime. The apprenticeship program is a comprehensive, accredited offering for CNC machinists, welding and mold building. The educational benefit allows employees to take job-related courses at the local community college.
The company’s apprenticeship program is well-established. “The first Franchino Mold employee completed an apprenticeship in 1969,” said Rusthoven, “and our apprenticeship program has been in its current hybrid form since 2011.” Of the company’s current workforce totaling 85 employees, 26 have gone through the apprenticeship program. Interest in apprenticeships seems to be on the rise – a welcome development for companies that need trained, skilled workers. “There has been an uptick in participation,” he said. “Enrollment in the machining programs at our local career centers are all wait-listed, and this is where we draw the majority of our apprentice candidates.”
Retention
It takes intentional policies and valuable benefits to retain a workforce. FMEC demonstrates its commitment to employees in a variety of ways, including the possibility of specializing in a role or gaining a broad understanding of the operation. “We have a lot of opportunities now available,” Rusthoven explained, “as our seasoned workers are retiring. New hires and current employees can specialize in a specific area or cross-train across multiple work centers.”
The company provides many other retention incentives. “We strive to offer a clean, safe and enjoyable working environment,” said Rusthoven. “We offer flex schedules, annual performance reviews, and competitive compensation and benefits.” FMEC’s benefits include health insurance, a dental allowance, reimbursement for prescription safety glasses, short-term disability coverage, paid time off/vacations and holidays, a 401(k) program with matched funds, tuition reimbursement and a tool/equipment purchase program.
“We strive to be above average when it comes to our benefits package,” Rusthoven said. “The company’s tool/equipment purchase program is another valuable benefit. It is like an interest-free loan for employees to purchase required tools for their job.”
In today’s tight job market and amid a resurgence in manufacturing, employers wishing to expand and protect their workforce would do well to consider the many ways that FMEC attracts, trains and retains its valuable employees. n
More information: www.franchino.com