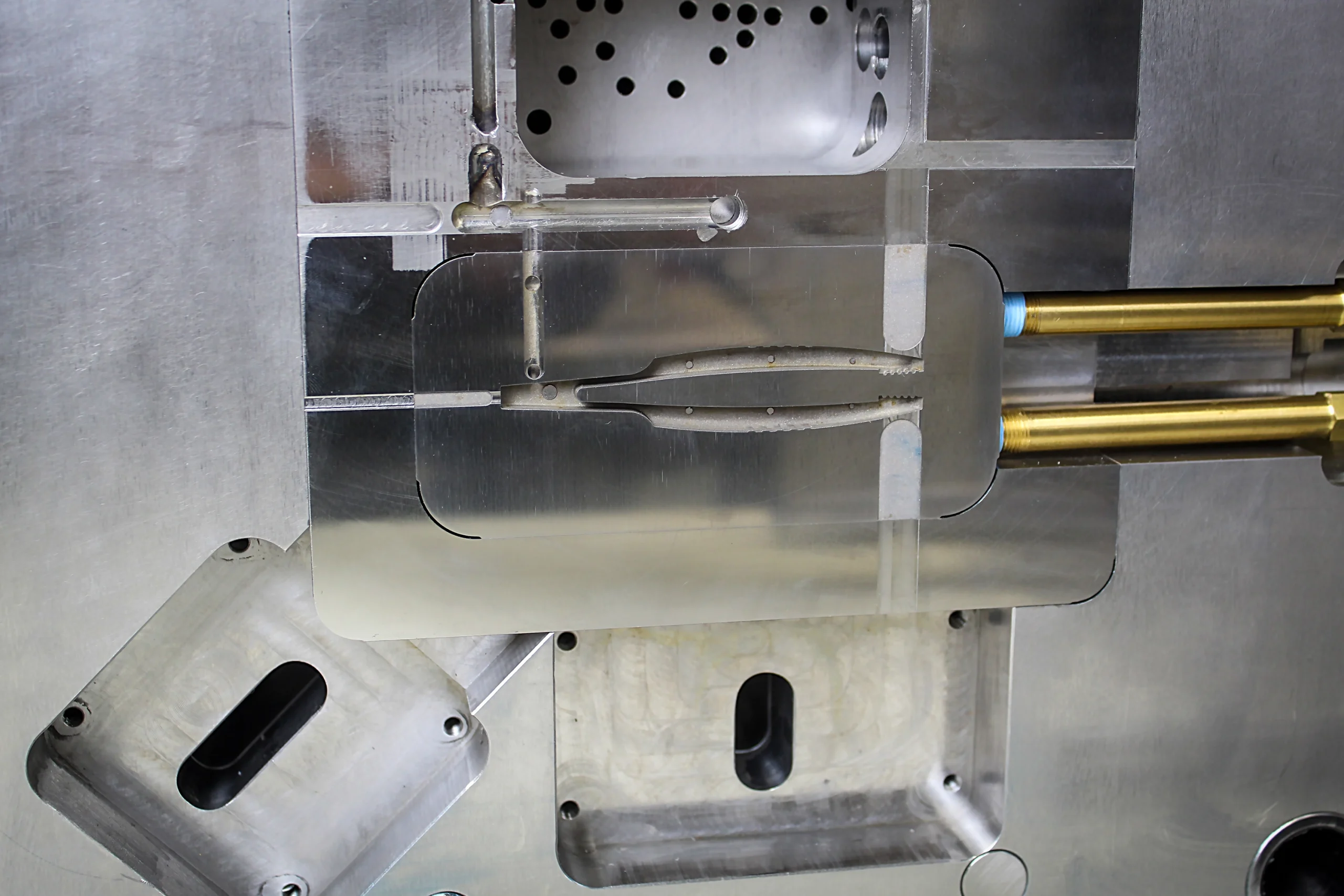
by Scott Kraemer, senior application engineer, Mantle, Inc.
According to recent market research1 from SmarTech Analysis (Crozet, VA), metal additive manufacturing grew last year by 16% to $3.9B. This growth brings rising opportunities that metal 3D printing technologies can offer to mold manufacturers.
Metal (and plastic) additive manufacturing capabilities consistently are finding their way into mold manufacturing companies. At Mantle, the company has collaborated with a number of mold builders to learn more about how its technology can enable mold builders to simplify the mold building process and shorten lead times for prototype, bridge and production tooling. Some of their insights will be shared in this article
In April, I moderated a session at the 2022 AMBA Conference with panelists Ray Coombs of Westminster Tool, Amanda Wiriya of Wepco Plastics and Mike McLean of Byrne Tool & Design to give attendees some perspective on additive manufacturing in general. For this article, I’d like to drill down into some of the questions routinely fielded about 3D metal printing for injection mold inserts using Mantle’s TrueShape process.
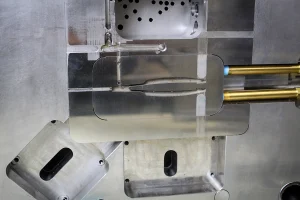
How does this technology compare to other metal additive manufacturing processes?
When EOS introduced the EOSINT 250 based on direct metal laser sintering in 1994, metal 3D printing was off to the races. Since then, the industry has grown to encompass various material extrusion, powder-bed fusion, hybrid powder-bed fusion and binder jetting systems.
The Mantle process is a hybrid that combines material extrusion with subtractive machining. The equipment extrudes a paste containing metal particles in a liquid carrier, building a part layer-by-layer. As each layer of the paste is extruded, it is heated and dried to remove the liquid carrier.
The insert then is machined immediately after each layer has been dried. This action refines the surface and enables the addition of features. After the part is printed and machined, it’s placed in a high-temperature furnace where the part is heated to just below its melting temperature. At this temperature, the metal particles fuse and the part sinters, resulting in a dense, strong metal part. Surface finishes of 1 to 3µm Ra often meet toolmakers’ requirements without the need for machining, meaning there is little to no post-processing required.
Integrated software coordinates all of these processes for automated tool path creation. In practice, this process has removed over 50% of the lead times required for both traditional and additive tool builds.
Other metal additive manufacturing processes rely on loose metal powders, lasers and electron beams. Several also rely on support structures that must be cut off and undergo a separate debinding step to eliminate the unwanted material. In contrast, the technology described here leads to tighter tolerances, better surface finishes and stable tool steels.
For more detail, the full metal AM spectrum of technologies was compared in a blog post2 illustrating the benefits and limitations of each process specifically as related to tooling. While many of these technologies have found success in niche applications, the approach described above overcomes limitations regarding post-processing, tolerances and surface finishes.
Why are mold builders considering this technology?
During the 2022 AMBA conference session, all three panelists commented that additive manufacturing was more than simply a means to attract new business. They viewed it as an investment in their future. Various molders and mold builders have echoed this sentiment, seeing metal AM capabilities as a means of solving the challenges of reduced lead time, scarcity of highly skilled labor and finding a way to accommodate customers looking to re-shore their tooling.
In addition, the lack of skilled labor in toolmaking and other metalworking disciplines means that experienced toolmakers’ time is valuable. Having a system that automates tool path creation and reduces the number of steps required to produce a tool frees up senior technicians to work on more projects.
Many customers believe using additive manufacturing will positively impact their current business models by enabling them to decrease lead times and increase volumes. Westminster Tool (Plainfield, Connecticut), for example, has just installed a Mantle unit in its facility after conducting numerous tests to prove its capabilities.
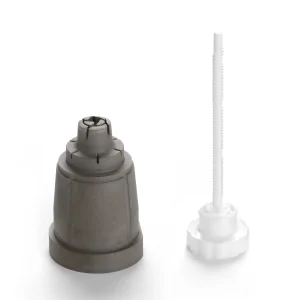
In one such test, the team at Westminster was able to go from concept to first off tool (FOT) medical parts in three weeks. Being able to dial in the process ahead of production using the Mantle inserts was another benefit noted by the company. Because the steel inserts can handle the tough-to-mold material used in production, all molding parameters could be transferred to the production phase.
Provide a real-world example in which a mold manufacturer used Mantle inserts.
Westminster Tool performed the test mentioned above before installing its first system. It represents a great example of how inserts are utilized in an existing mold manufacturing environment.
Earlier this year, another project required tooling inserts (core and cavity), so the team at Westminster could quickly mold medical forceps sample parts from a highly glass-filled, bio-based PA11 material from Arkema. According to Westminster Tool’s manufacturing engineer, Eddie Graff, a traditional aluminum prototype tool would present difficulties in molding the highly glass-filled PA11. Graff designed the tool inserts to include conformal cooling channels to control the cavity temperature more effectively, which is critical to molding this particular material.
The printed inserts held a tolerance of +/- 0.0015”. Because they were made with H13 tool steel, the inserts allowed Westminster to add a sub gate so the company could mold thousands of parts without the risk of gate erosion.
What about machining and welding performance?
Precision Laser Technology (PLT) tested four bars printed in H13 tool steel. These tests demonstrated that machining, grinding and laser welding operations for the bars were equivalent to the same operations with traditional tool steel; they required no changes to the standard operations, and the results were equally successful. For grinding, before and after welding, the surface appearance was indistinguishable from conventionally manufactured H13. There was zero evidence of pitting, and there were no signs of wheel loading or heat generation.
Ron Natale, PLT co-owner, explained that it was a seamless experience and didn’t disrupt any of the processes in his shop. He needed no special tooling or alterations to the process because of the material. He reported that performance was consistent with conventional H13 across all machining and welding processes and outcomes, including surface appearance, machinability and performance.3
Which moldmaking applications are possible with this technology?
With this process and tool steels, tooling inserts can create prototype, bridge and production tools. A medical device manufacturer reduced the lead time for a prototype tool by eight weeks, which enabled it to accelerate product development. Tessy Plastics has been running a production tool that uses Mantle inserts for over one year, and the inserts have survived over 1.25 million cycles to produce parts for deodorant packaging. All molded parts have passed stringent quality inspection, and the mold continues in operation.
In addition, conformal cooling channels can be added to any prototype or production tool. These channels can dramatically reduce cycle times and facilitate the molding of challenging materials where precise temperature control is required.
Scott Kraemer is a senior application engineer at Mantle. He is passionate about toolmaking and has spent his career as a mold designer, tooling engineer and injection molding specialist at companies including Innatech, L&L Products and PTI Engineered Plastics. For the last eight years, Kraemer has been at the forefront of applying 3D printing technologies to the tooling industry and has worked with many leading metal and polymer 3D printers.For more information, visit www.mantle3d.com.
References
“Additive Manufacturing Industry Grew 18 Percent in 2021 to $10.6B Reports SmarTech Analysis; Projects $50.8B By 2030,” April 5, 2022, https://www.smartechanalysis.com/news/additive-manufacturing-industry-grew-18-percent-in-2021-to-10-6b-reports-smartech-analysis-projects-50-8b-by-2030/
“Not All Metal 3D Printing Technologies Are Alike,” June 10, 2021, https://www.mantle3d.com/not-all-metal-3d-printing-technologies-are-alike/
“Mantle to Showcase Three Case Study Collaborations at PTXPO and AMUG,” March 28, 2022, https://www.mantle3d.com/mantle-to-showcase-3-case-study-collaborations-at-ptxpo-and-amug/#:~:text=Machining%20and%20welding%20like%20tool%20steel