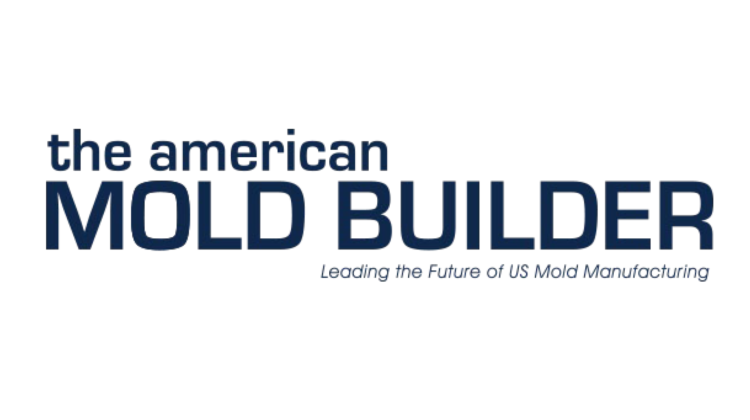
by H. Alan Rothenbuecher, partner, Benesch Friedlander Coplan & Aronoff LLP and Katie Berens, summer associate
As a mold builder, it is important to minimize risk to remain successful and profitable. This is no easy task – this requires knowledge of what risk areas to target, and how to best reduce each form of risk. The ability to avoid common costly pitfalls in contracting can help mold builders stay competitive in the industry and stable in their business financials. Below are five key risk areas to which every mold builder should pay attention when drafting a new agreement or renegotiating the terms and conditions of an existing contract.
Leverage price adjustment clauses
Price adjustment clauses are contract terms that provide for the higher or lower pricing of goods, dependent upon certain conditions. These clauses mitigate uncertainty in pricing of commodities, as they can protect against financial exposure from price fluctuations. When executed properly, these clauses can insulate parties from costs resulting from inevitable market volatility. Price adjustment clauses can help foster long-term contractual relationships, as they minimize the need for future ongoing negotiations on the same pricing issues. Use of these clauses also can reduce the likelihood of contractual breach, as they embed a plan into the agreement to address how the terms of the exchange will shift to accommodate sudden changes in the market.
In legal disputes, courts commonly hold price adjustment clauses enforceable in agreements between sophisticated parties. Generally, a sophisticated party is aware of and understands the bargain to which it is agreeing. Notably, parties may specify their status as sophisticated parties within the terms of their contract, which can further the likelihood of enforcement of a price adjustment provision in a case of dispute.
Mold builders should utilize these terms in their agreements to minimize potential financial loss when facing a market downturn. Incorporating a price adjustment clause into the agreement likely will require some negotiation. Any such clause should include a defined price index designed to respond to material changes in the market. This clause should specify a maximum and minimum price range for the price adjustment.
Be aware of the mold builder’s lien
A lien is a legal right against another party’s assets that can be exercised to ensure fulfillment of an underlying debt or obligation. Mold builders may need to exercise their lien rights in cases of non-payment for materials or services rendered. Mold builders must ensure that their lien rights remain protected under any agreement into which they enter. Mold builders should familiarize themselves with the laws in their state governing mold builder lien rights to understand what measures can be pursued to secure payment for materials or services provided if needed. Often, a UCC financing statement must be filed for a mold builder to protect its lien rights.
Mold builders also should be aware of and look out for the lien release agreement. A lien release is signing away the ability to exercise the mold builders’ lien rights, such that they may not pursue certain claims against the other party in the case of a future dispute. Any such release should be negotiated and, if agreed to in exchange for payment, should be written as narrowly as possible. Further, a lien release can incorporate certain conditional language to better protect the mold builder’s interest – i.e., conditioning release upon actual receipt of payment. Exceptions also can be written into release terms, which can help prevent the mold builders from learning that their rights have been waived at the moment when they need to exercise them.
Disclaim implied warranties
A warranty is a promise that a seller makes to a buyer about the quality and useability of the goods being sold. Under the Uniform Commercial Code (UCC), a set of laws that apply to all commercial transactions in the United States, certain warranties may be read into a contract – even though they are not expressly written in the agreement. Mold builders can prevent future liability in a potential dispute by visibly disclaiming such warranties within any supply contract.
Common implied warranties include merchantability, fitness for a particular purpose and non-infringement. Merchantability is a guarantee that the molds sold will serve their ordinary purpose and satisfy the buyer’s reasonable expectations. Fitness for a particular purpose means that the mold will serve an intended purpose that is clear to both parties of the sale. Non-infringement is the assurance that the molds sold are not infringing upon existing intellectual property rights.
Mold builders should ensure that they disclaim as many implied warranties as they can. To be upheld under the law, any disclaimer of implied warranties within a contract must be visible and obvious. If the wording is unclear or the term is hidden within the contract, it is more likely that a court will hold the disclaimer unenforceable in a dispute. Mold builders need to ensure that there will be no responsibility for any defects that occur beyond the actions in their control. Mold builders should put this safeguard into their contracts to protect against the risk of financial liability from a promise that was never expressly made.
Include the proper Incoterms
When goods are transported between seller and buyer, certain logistics must be clarified to ensure a smooth transfer. Misunderstandings can present roadblocks in a transfer of goods that lead to surprise financial costs, as well as frustration and delay of business. Incoterms address this issue by establishing universal rules to clarify the responsibilities of each party to a transaction that involves the transport of goods.
The International Chamber of Commerce (ICC) promulgated Incoterms in 1936 to promote clarity in commercial transactions and provides periodic updates to them to incorporate changes in trade practices. Incoterms clarify who is responsible for costs and management of each logistical step of a transaction, such as shipping, insurance, documentation and customs clearance, among others.
There are 11 Incoterms that may be used in trade contracts to allocate risk and responsibility. For example, EXW (Ex Works) provides protection to a seller by requiring the buyer to assume all risk and transportation costs. Under FCA (Free Carrier), the risk passes from the seller to the buyer at the agreed-upon point of delivery. FOB (Free on Board) means that the seller is obligated to deliver the goods on board a ship for the buyer.
Incoterms are optional – parties must opt into them by including the proper terms in their agreements, and those agreements must specify the version of Incoterms to which the parties are referring. Mold builders must be sure to use the right Incoterms within their contracts to minimize their risk in the shipment of molds to a buyer.
Under the terms of an agreement, buyers should remain responsible for all that is in their control in a transaction. It is critical for sellers to select terms that only place risk upon the actions that they control.
Incorporate limitation of liability clauses
Lastly, mold builders should include limitation of liability clauses in their agreements to eliminate the risk of financial exposure for actions of the buyer. A limitation of liability clause limits a mold builder’s potential for exposure on a claim related to the molds. Include contract terms that say the mold builder will not be held responsible for any misuse, mishandling or improper storage by the customer.
Misuse is when a molder uses the mold improperly, or for an incorrect purpose. Mishandling occurs when a molder uses the mold incorrectly or ineffectively. Similarly, improper storage is the exposure of the mold to conditions that damage its effectiveness because of the molder’s incorrect handling of the mold. Limitation of liability clauses also can be used to exclude forms of damages that can be sought in a potential lawsuit, such as consequential, incidental and punitive damages.
Mold builders should incorporate clauses into their agreements that eliminate their liability for actions that are entirely within the buyer’s control, and that exclude these forms of damages from potential recovery in a lawsuit against them. Under the UCC, limitation of liability clauses must be clearly displayed in consumer contracts and easy to understand to be enforceable.
Mold builders should review their agreements and consider the extent of all clauses to protect against being held responsible for unforeseen consequences beyond their control as sellers.
Alan Rothenbuecher general counsel for the AMBA organization and a partner with the law firm of Benesch, Friedlander, Coplan & Aronoff LLP. Rothenbuecher concentrates his practice in the plastics industry and proactively addressing challenges faced by industry companies. For more information, contact Rothenbuecher at 216.363.4436, www.beneschlaw.com or ARothenbuecher@beneschlaw.com.