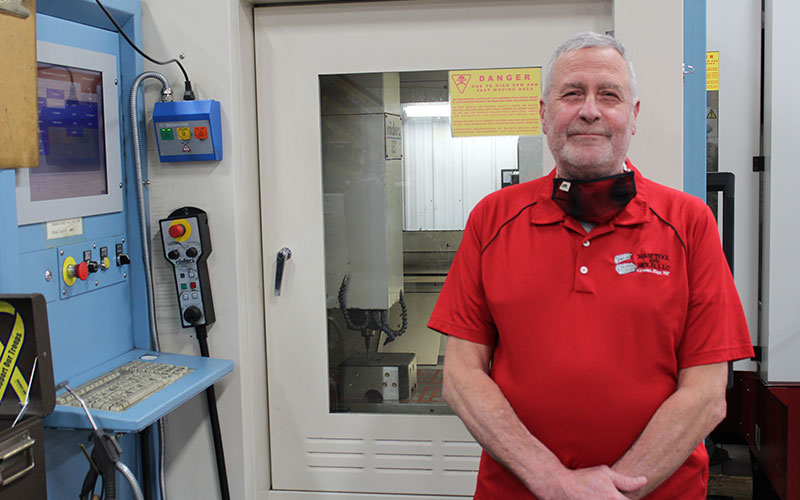
by Liz Stevens, contributing writer, The American Mold Builder
The accumulated knowledge at a mold building operation is a unique and valuable commodity. Experienced team members are veritable walking encyclopedias of the ins and outs of mold building, from the associates with decades of material procurement experience, to the engineers with in-depth CAD and design expertise, to the toolmakers who use their reservoirs of knowledge to synergize computer-based part models, mold designs and blocks of new steel into working molds. For any moldmaking operation to survive and flourish, that priceless pool of knowledge must be tapped for each new job, and for many jobs the process of reaching back into history in order to plan for a successful future begins at the estimating phase.
Carl Jacobsen is an estimator/tooling engineer at M&M Tool and Mold. The Green Bay, Wisconsin-based company crafts small- to medium-sized injection molds, some of which require ITAR compliance. Jacobsen, who began as a toolmaker at a bench, has been at M&M for 10 years. Keenly aware that successfully estimating and quoting a new job today depends upon finding, reviewing and incorporating the information from prior similar jobs, Jacobsen is on a quest to create a system for capturing and indexing his company’s tool build history.
When Jacobsen came to M&M, the company had a seasoned general manager who had worked his way up from toolroom lead. When it came to estimating new jobs by looking at earlier jobs of the same type, the GM was a great resource for estimators like Jacobsen. “He had an excellent memory of every tool we built during his tenure with the company,” said Jacobsen, “and could point the estimating personnel to who the customer was, and even what the job number was. This information allowed easy retrieval of financial job information for estimating similar tooling.”
When the general manager left the company, Jacobsen had a few years of his own accumulated tool build knowledge and also had veteran toolmakers at the company to consult. But Jacobsen is aware that time, including other people’s time, is money. “I do have other people in the shop that I can pick their brains,” he said. “But rather than having to go out and bug a toolmaker on the shop floor or interrupt somebody else to take a look at this and say, ‘Have we ever done anything like this?’, I would like to have a repository that I could search to see if that is something that has been done.”
Jacobsen also prefers to not rely solely on employees’ memories for this crucial information, because one never knows when an employee might no longer be available. “Whether that loss is through somebody taking a different job,” he said, “retirement or whatever, there are so many areas where people have knowledge that they gained and that is not well-recorded in the company.”
What Jacobsen would like to have for capturing this data at M&M Tool is a searchable photo index of past projects. “As a starting point,” he described, “I am looking to capture a high-level view based on molded part geometry, mold design and overall profit and loss performance on the tool build.” The photos would be a collage of the part, the tool and the company’s job detail report. The search criteria would be metadata assigned to the images.
With this type of system in place, searching for historical build data would be fairly straightforward. “The first thing I would base it on is part size by cubic inches of volume,” Jacobsen explained. “Then I would describe a shape, and then the required type of actions – such as slides, lifters, unscrewing – and finally I would choose a general mold classification – such as a conventional type of mold, or molding over inserts, or LSR molding or zinc diecasting.”
M&M added an ERP system about a year ago, but it does not have the repository features that Jacobsen seeks. He said that customizing the ERP system for his needs would be a costly and lengthy modification and, even if it were cheap and quick, an ERP-based system would not be an ideal solution. “Even if I could get this search index somehow incorporated into the ERP system,” Jacobsen said, “our ERP system is cloud-based. Several of our customers and the parts that they have us build tooling for are covered under ITAR so I can’t share that data to a non-secure external server.”
In considering creating an in-house system using commercially available software, cost remains a factor. Jacobsen considered a software package which is available on a per-seat subscription basis. But for M&M, at least four licenses would be required to cover all of the employees who do estimating, making an affordable-for-one solution not so affordable for multiple licenses.
In implementing any type of system, the challenge of data integrity will always crop up: GIGO – garbage in, garbage out. That’s a rather unflattering way of saying that the quality of data upon which a new system is built – complete and flawless data or holey-as-Swiss-cheese data of questionable accuracy – dictates the quality of data that is subsequently retrieved from the system. Jacobsen sees a handful of challenges in importing historical data and then relying upon it for generating M&M’s new tool building estimates. “The need for accurate build data (no double charging of hours) and the need to redefine how certain activities have been charged to jobs are challenges.”
Build data that might include double reporting of hours stems from how M&M has recorded and distributed delivery time with the company truck with the new accounting system. In the case where a delivery driver picks up or delivers multiple tools for different customers during one trip, the system logs all the delivery time to each customer visited, creating an erroneous
delivery hour report which must be corrected when billing the customer. Before importing historical data into the new system that Jacobsen envisions, work would be required to find and correct any delivery hour reports that slipped through the cracks and remained uncorrected. Without this correction, new estimates based on this data could easily include an inaccurate delivery hour report.
Another issue that Jacobsen sees as a potential for inaccurate job estimates is one that stems from how toolmakers record (or don’t record) time classified as rework. Jacobsen sees this as a reflection of human nature, not as a comment on the associates at M&M. When a block of steel has to be scrapped due to an error that occurred during one of the many phases in building a tool, the project must track the amount of time to recreate (rework) a new block of steel to replace the scrapped one, and workers sometimes fear that charging time to “rework” will reflect poorly on them. But if they do not accurately record rework hours, it is not possible to accurately determine the cost of building the tool with its rework clearly noted so as not to skew any future estimates based on this job.
Another challenge in tackling this type of company-specific repository project is how to define robust search criteria, how to ensure the integrity of metadata each time new records are added and how to thoroughly test the newly created system to see that searches work properly (without returning too few or too many possible results).
For Jacobsen, the quest for a searchable photo index of past projects remains a work-in-progress. “I have been thinking on how to create and search the index for just over two years,” he explained. “I have done several re-writes of the search criteria to generate relevant search results.” As with many busy moldmakers, M&M has kept Jacobsen hopping with estimates for new jobs, leaving little time for his quest. “Internally, this project has not elevated into my ‘whirlwind’ classification, so I am working on it when time and workload allows.”