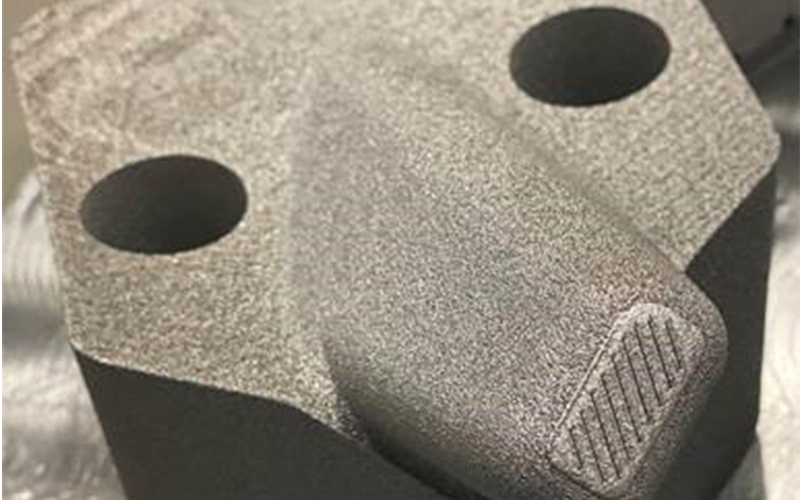
by Liz Stevens, writer, The American Mold Builder
Additive manufacturing is growing steadily, having evolved beyond its initial applications for creating 3D models and producing specialized, very low-volume parts. For mold builders, 3D metal printing now offers components for conformal cooling, venting and hot runner manifolds, with more developments on the horizon. The American Mold Builder talked with Jason Murphy, president of the additive tooling company Next Chapter Manufacturing (NXC), Grand Rapids, Michigan, about the current state of 3D metal printing. Marcin Zajac, engineering manager at A1 Tool Corporation, Melrose Park, Illinois, and Steve Michon, owner of Zero Tolerance, LLC, Clinton, Township, Michigan, also were interviewed about their experiences with NXC to design and build conformal cooling components.
Jason Murphy founded NXC five years ago to apply the special qualities of 3D metal printing for the benefit of plastic injection mold builders and their plastics processor customers. With a background as a traditional mold builder, RJG-certified master molder, injection molding plant manager and owner of a traditional mold building shop, Murphy first gave additive manufacturing a whirl 24 years ago and has kept his eye on it ever since. “I always saw 3D printing as an option,” he said, “ for something like cooling, where it needs to be in a mold, and to get good part quality over what was conventionally available, such as milling and drilling a water line.” Until recently, additive technology, however, was not yet fully capable and reliable. “There were a lot of cracking issues,” he explained. “It was not capable of producing really good, porous vents. And there was leaking and other problems that you really don’t want in a cooling part.” Murphy said that it wasn’t until the last five to seven years that things improved enough for additive to be reliable for tooling. As he watched the technology improve, Murphy developed tool steel powder recipes specifically for 3D production of injection molding components.
NXC uses directmetal laser sintering (DMLS) additive technology, a process that Murphy described as one of the oldest, most mature and refined 3D metal printing processes. The company’s additive printers build layer by layer, laying down and laser sintering metal powder to produce very hard, fully dense and solid steel components that are finished with heat treatment and stress relief. The metal powders in use are current-day incarnations of MIM powders – previously used for metal injection molding – which are created through gas atomization. The largest printer at NXC can produce 12” x 12” x 16” components, and Murphy is awaiting delivery of a new machine for producing even larger parts.
Conformal Cooling – Made for Complex Geometry
As the designs for parts have become more complex, including more structural details and features such as ribbing, conventional cooling componets now often are inadequate to the task. Complex geometries and very tight spacing often cannot be effectively cooled with traditional line-of-sight milling and drilling. “What 3D printing does over conventional milled and drilled water lines,” said Murphy, “is provide the freedom to get ejection, venting, sub-inserts and difficult part geometry; you are not limited by straight line-of-sight, milled and drilled water lines. Conformal cooling allows you to not only navigate around the contour of the part, but also around all the other features, such as slide pockets, ejector pin holes, core pin holes and other sub-inserts found in increasingly complex tools.”
Additive manufacturing of conformal cooling also can deliver superior part quality via balanced cooling, and the cooling circuitry can be designed with changes in shape to match the available real estate in a mold. “Those are things that are important for moldmakers to account for when they are designing,” Murphy said, “and with 3D printing of conformal cooling, there really are no limitations. We can pretty much print anything; there are some optimal geometries or things that we know from experience, but folks can build very complex channels. In complex channels, the surface area of the
channel can be changed by adjusting the profile of the channel for better cooling.” At NXC, Murphy strives for a happy medium, “something that you can easily maintain in production with simple ultrasonic cleaning but also something that is very high performance for balancing the cooling rate and giving very good cycle times.” Murphy has seen conformal cooling deliver dramatic improvements in cycle times – a decrease of 20 to 80% over conventional cooling.
NXC Designs and Builds for Zero Tolerance
Steve Michon of Zero Tolerance explained that a customer asked for a mold for a 30-round .22 rifle magazine. The part’s geometry – a thin, curved and ribbed shape – was one that would have been very difficult to cool with conventional cooling. “There was limited space and a big need to make the cooling circuit correct,” said Michon. “We could have drilled some holes as straight as we could and made a small connection in there, an in-and-out straight-line circuit, except that this would be limited by the size of the drill, and there was a risk to doing that in hardened steel.” Michon said that the alternative was to do a 3D-printed version that could contain any type of cooling circuit to follow the contours of the part.
Zero Tolerance had used additive to print composites and some 3D plastics but did not have experience with 3D printing metal. With the customer’s buy-in and with some skepticism, Michon turned to NXC to see what Jason Murphy could design and print. “We built the cavity, the core and the mold base,” Michon explained. “NXC printed the areas that we couldn’t do conventionally. It printed the slide features – the only curved parts – and left stock on them after printing so that the parts could be machined and benched to meet the customer’s requirement for a smooth finish.”
Murphy described how NXC handled the job. “This was a perfect example of something that would not be able to be built traditionally with a drilled water line. NXC gave us the core to build to, gave us the ins and outs for the water, and said ‘okay, you guys take it from here.’ For this curved magazine clip, we could only drill in maybe a third of the way before we would break out into the side wall. To deliver consistent cooling and an even flow, we had to follow the contours of the part.”
The part was wide in one direction but very narrow in the other direction. “Usually in conformal cooling,” said Murphy, “we are constrained in one direction but we have space in another direction so we can change our cooling channels to be conformal and also change the profile of the channel.” Murphy designed elongated cooling channels that changed shape as they wound through the space available in the part, flattening and widening as needed to create a consistent flow.
“The project turned out well,” said Michon. The parts produced by NXC looked and felt just like regular tool steel. “The initial pieces came out like casted parts, even though they were much better than casted parts. When we machined them, they machined just as good as the stainless steel that we would use to make it from a solid.” As 3D-printed parts that are layered, there was some witness of that but it was simply surface cosmetics. Internally, the parts were solid. “When we got the mold completed,” said Michon, “the stainless steel printed slides with the curves and the water circuits were great. They would reduce the cycle time for the customer quite a bit.”
Had NXC not been available, Zero Tolerance would have had few other options for producing a part with this challenging geometry. “We could have used a different material for the center core, such as beryllium, which is a very good heat sink and pulls heat out quickly,” Michon said, “but it is a lot more expensive. The customer was looking to make a tool that would last a long time, calling for a hardened steel production style. We probably would have searched out another 3D printing source or investigated getting a machine for ourselves.” But with a limited need for 3D-printed metal parts, turning to
an outside source such as NXC made more sense than purchasing new technology and learning the ins and outs of additive design and printing.
NXC Designs for A1 Tool
Marcin Zajac at A1 Tool has experience in designing and printing 3D-printed mold components and also has worked with NXC on a number of projects. A1 had a customer
that wanted to improve an existing mold and wanted to see what NXC would recommend for an improved conformal stainless steel cooling layout. Simultaneously, Zajac designed an improved conventional copper alloy cooling circuit
as another option.
A1 performed analyses on the two designs and found nearly identical results. The customer ultimately chose the conformal cooling option. “The project NXC worked on with A1,” said Murphy, “was a great collaboration as we were able to take machined base inserts and 3D print the conformal cooled portion on top. This was a great option for implementing conformal cooling while keeping costs within budget.”
Based on his experience with conventional and conformal cooling circuits, Zajac offered some advice for moldmakers who are considering whether to pursue additive manufacturing of conformal cooling. “Which one is better?” he asked. “Is simple better? In engineering, when we design, we try to KISS (keep it simple, stupid). The simpler it is, the less maintenance, the longer it runs and the easier it is to maintain. I am not saying that nothing calls for conformal cooling but we have to be really thoughtful and conscious of the decision.”
“One thing that I would say is the biggest drawback of conformal cooling,” said Zajac, “is that it can be very complicated. For example, molders cannot stick a rod into it and clean it out if it gets clogged. And moldmakers have to invest money into monitoring the flows and filtration.” In his experience, preventive maintenance on conformal cooling circuits may require sending components off-site for cleaning, resulting in production downtime or the purchase of extra components to avoid downtime. Zajac also felt that complicated conformal cooling designs sometimes leave little room for subsequent engineering changes to the mold. Overall, however, Zajac favors conformal cooling when it is appropriate. “If the fit is good, it will perform miracles and improve the cycle times.”
The Takeaways
Steve Michon’s experience with 3D-printed conformal cooling was very positive. “I would recommend trying it,” he said. “A lot of people think, ‘We will just buy a machine and do it ourselves,’ but for 3D printing for metal, it is not as easy as it sounds. NXC has a lot of experience and it has a good reputation.” Michon added that, budget allowing, it is worth trying. “Most of the time, if we are molding the parts, the savings are there. If we are the tool builder, the choice has got to be driven by the customer that is doing the molding.”
“I think it is something that people in the industry don’t feel is a viable option,” said Michon, “because it is not widely used. The way we conventionally do things, moldmakers think we can do the job cheaper but additive really is not that much of a cost now. For us, the difference in cost was 15 to 20% to do this out of standard vs. 3D-printed. We still had to machine it afterward but to get that circuit in there, we would never have gotten that done.”
Zajac summed up his thoughts on additive for cooling circuits: “There are applications for 3D-printed conformal cooling,” he said. “It can be great, but we have to plan for it, invest in it and be very conscious about when to use it.” He offered an ideal scenario: “Let’s say we are working with a part that has been proven out in the field and are building a ‘tool two.’ We are going into it knowing the issues of the original tool, and we are upgrading, to get a better-running tool. We know that this original tool functions as it is but that we can get a better cycle out of it if we make this change. To me, a tool two – going in with lessons learned or a very, very similar product – is a great choice for 3D-printed conformal cooling.”
Murphy agreed that moldmakers should not leap into buying their own 3D-printing technology or expect additive manufacturing to be a simple fix or a slam dunk for every project. “For conformal cooling,” he said, “we are looking at the cooling efficiency and we also are looking at the flow. We use computational fluid dynamics regarding the mold flow to make decisions about where the hot spots are in the tool, and we also simulate the actual build of the 3D printing.” Murphy has seen the results when moldmakers apply additive manufacturing without a thorough understanding of the discipline. “We have seen parts come in that have to be redone because they were not designed properly. They still look like they are milled and drilled water lines, even though they were made with 3D printing.” To use additive manufacturing effectively requires approaching projects from an entirely different angle. “We don’t build buildings from big blocks of steel,” Murphy said. “We build them with I-beams and structural girders and things that have structure to them. That is kind of how additive is – we need to think more structurally than just whittling away from a big block of steel.”
NXC currently specializes in conformal cooling and venting components. “People are wanting better venting, improved part quality and bigger tooling,” he said. “Right now, probably one of the fastest growing areas is the venting technology.” The company now also is 3D printing hot runners. “I have an extensive background in hot runner technology. We are 3D printing hot runners and manifold systems that are fully balanced and have no dead spots in them. Instead of milling or drilling the circuits for the melt, and then finding a dead spot or a T that would cause shear in the material, we actually can make a nice curve, eliminating dead spots.” Overall, Murphy remains focused on creating value. “We go back to the biggest problems in the industry, and then ask how we can attack those from the molders’ perspective and how we can help the molders out. That benefits the moldmakers and everybody succeeds.”