By Rachael Pfenninger
AMBA Project Manager
Understanding how to schedule jobs and maintain efficiency in any mold manufacturing facility can be critical to a business’s ability to win orders and keep existing customers – both of which significantly impact the bottom line. This is why any loss of efficiency (particularly in job programming) is worth tackling as soon as it’s identified. With that said, there are many ways to program jobs efficiently, and no mold builder does it exactly like any other.
For this reason, AMBA surveyed its members to benchmark programming efficiency in their shops. Gathered data included workforce representation (including total employees vs. CNC programmers and set-up operators), preferred programming software, shop floor programming vs. offline programming, the efficiency of certain programming methods for repeat and new jobs, and recent investments in technologies and/or machines to improve efficiency.
Of the 63 respondents surveyed for this report, the largest geographic concentration represented the Midwest US region. The top markets served included the consumer products, automotive and medical/optical/dental markets. Most rely heavily on new jobs – most mold builders reported that less than 50% of their work included repeat jobs. Overall, average lead times for those jobs tend to be in the nine- to 12-week range, although most shops have a small percentage of work that falls both below eight-week lead times and above 17-week lead times.
Regardless of reported annual revenue or top markets served, the most popular programming software amongst respondents included Mastercam, 3D Systems/Cimatron and Autodesk (Powermill). However, when correlated to the number of CNC programmers and set-up personnel on staff, those using the Autodesk (Powermill) software employed – on average – double the number of programmers and set-up personnel of the other two software options. (See Chart 1.)
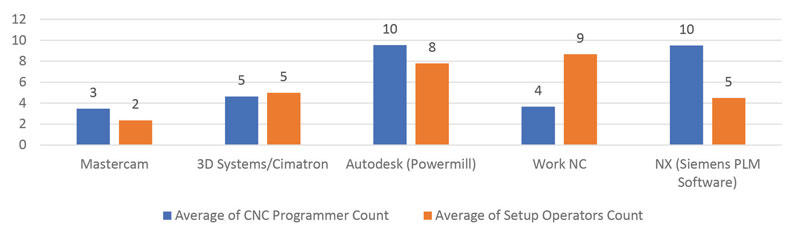
Overwhelmingly, respondents indicated that CNC programmers (rather than set-up operators) were expected to program the majority of jobs in the shop. Interestingly, nearly half of all respondents indicated that their CNC programmers had some level – up to four years – of experience in designing, while another quarter employed CNC programmers with up to four years of experience in moldmaking.
When examining machining, nearly 75% of respondents shared that their CNC programmers had five or more years of experience. (See Chart 2.) These levels of experience indicate that there is clearly some value in crosstraining, particularly if a company is having trouble sourcing qualified CNC programmers.
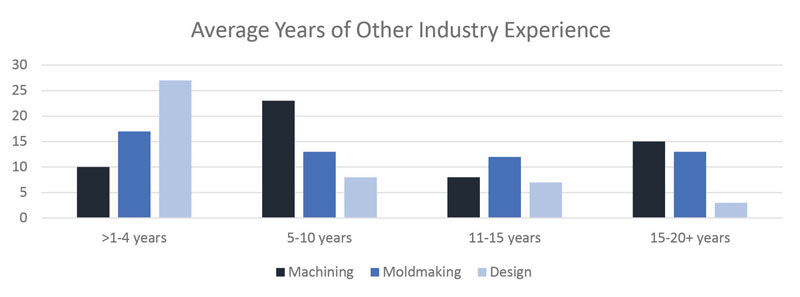
Unsurprisingly, respondents largely found that CAD/CAM programming is a more efficient programming method than either conversational or manual controls. However, several of those surveyed acknowledged that conversational controls can be relatively efficient, particularly for repeat jobs. Of those respondents who do prefer manual controls, most rely on repeat jobs rather than new work.
To purchase the full report, including a summary of what investments other mold builders are making to improve efficiency in their shops, visit https://amba.org/publications/browse/.
Key Tips to Filling Your CNC Programming Needs
If you struggle to find talented CNC programmers, the following steps could be worthwhile.
- Take a look at the capabilities of your programming software. With the right system in place, set-up operators with less knowledge could perform the same tasks and produce the same quality of work.
- Crosstraining can be a valuable way to expand your CNC workforce. If you have difficulty sourcing CNC programmers to fill new positions, consider existing employees in moldmaking, machining and designing.
- Mold builders tend to rely heavily on new jobs, which could be sucking up productivity. By sourcing more jobs that tend to be repeated, mold builders may be able to diversify the types of jobs in their shop, improve efficiency and decrease the workload of the programming staff.