By Brenda Clark, engineering manager
HASCO America, Inc.
Mold coatings are being used to improve tooling production life, extend time between scheduled preventative maintenance stops and reduce the necessity for mold release agents. Technology advances have improved wear- and corrosion-resistance properties, as well as resulted in increased hardness levels. Here, common questions about the use of mold coatings are answered.
Q: What are the primary advantages to using mold coatings?
The primary advantages to using mold coatings are slip properties or the coefficient of friction, a higher hardness surface, increased wear resistance and corrosion protection.
Mold coatings can improve the coefficient of friction from 0.45 up to 0.05 microns, allowing tools to function even without applying mold release. Most moving applications require a difference in hardness between moving materials. When similar materials are used, the difference can easily be accomplished by coating one of the two inserts. The higher hardness increases the wear resistance and aids in corrosion protection by extending component surface finish life.
With some coatings, the improvement of the coefficient of friction will allow the two moving materials to move freely even without added lubrication or grease. Some coatings even are applied to the mold assembly to assist further once the molded part is placed into a post-molding operation to ensure that operation is a success. Post-molding operations, such as painting or plating of a plastic part, require cleanroom parts free from grease and contaminates, even though the end part is not a true cleanroom product.
Q: What drawbacks are there? Are there certain situations in which mold coatings should not be utilized?
There are several processes for coatings (see Chart 1) used in injection mold assemblies. Over the years, drawbacks in certain coating types have required technology advancements to better overcome friction, withstand higher temperatures and increase wear and corrosion resistance.
The original forms of coatings – hard chrome and nitride – have been applied aftermarket to standard components or to create a layer of coating on a base material. This process allows the coating to actually build up and possibly delaminate, chip or flake off during production running of a mold. Higher temperatures, lack of grease or proper maintenance are additional reasons these older coatings fail. Higher processing temperatures can cause the coating and adjacent material to work harden. This will change the hardness rating between the moving components to be similar and potentially cause unwanted galling or wear.
Based on the specific mold build and the production life of the tool, it may not be economical to use certain coatings. When a tool has a lower expected production life, the added cost for specialized coatings may not be justified because of the shortened production time frame.
Q: What are some of the latest technical developments?
The DLC coating, or Diamond-Like-Carbon coating, is one of the latest technical developments in coatings. This coating is available from several suppliers and, as the process is different with each form of DLC coating, users should speak specifically with their suppliers as the processes should be handled by the experts.
The HASCO DLC coating is a PVD/PACVD form of DLC coating specifically created for HASCO standard components.
The optimum tribological property coating (see Image 1) is specially imbedded into the base material – not just applied as an added layer. The coating is applied using a lower application temperature while maintaining a higher service temperature to achieve the best coefficient of friction of 0.05 microns.
The base component material must be cleaned properly several times prior to the coating process. This cleaning process ensures that the coating will not chip off during production. If the coating does chip off, the process was applied incorrectly or not completed by the original supplier. The tolerance still is maintained on the component as the size is taken into consideration before coating to ensure the final component meets standard sizes. This process will embed and add a minute buildup on the component, allowing users to change from standard non-coated components to the new DLC-coated version without added rework in older tooling to help improve production.
Q: Are there common problem areas that may utilize coatings?
Most plastic material suppliers have design guides that will suggest the best coating/plating to use in a design for mold release for their specific plastic material. There is not a specific coating that will work for every application. For example, one plastic supplier suggests that when using a polypropylene material, the part will release better out of a mold with a matte finish vs. a high polish finish. Another mold plating service provided similar information: when using a diamond finish (high polish), if release is a problem, it may be a better choice to use a blast finish (matte). A nickel coating also could be used as it is slightly textured compared to a DLC coating, particularly when using materials like silicone rubber and TPE (see Images 2 and 3).
Mold design and build for function, rather than a sticking or wear issue, can utilize the new DLC coating as an advantage. Moving parts, such as leader pins and bushings or guided ejection to 2-Stage ejection, are all now available with the DLC coating already applied from the supplier. Users now have an off-the-shelf option readily available to install directly into a new mold. Users also may repair an existing mold with the coated version component to employ the advantages of DLC.
Q: How do coatings extend mold production lifespans?
Many benefits are achieved when the proper coatings can be used in tooling to increase the life of mold production. The corrosion resistance gained through coating application will greatly increase the tool’s wear resistance, allowing components to work longer within a mold with aggressive running material. With an increased amount of time between scheduled maintenance stops, the tooling has less downtime, leading to fewer times the mold must be pulled from the molding machine and reducing the possibility of damage to other areas of the mold or molding machine.
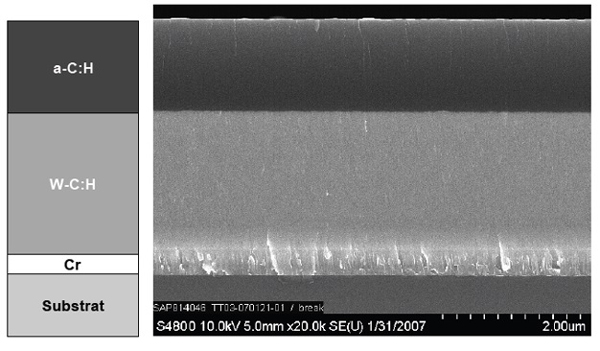
Q: Are there cost savings and/or production efficiencies that are realized when coatings are used?
There are valuable cost savings and production efficiencies that are realized when using specific coatings in specific areas of tooling. As mentioned prior, less downtime equals higher production, which means more profit, not to mention more efficient cycle times. This can save machine hours and employee man hours – and, time is money.
Another source of savings is realized when molding can be allowed in a cleanroom without the requirement to remove unwanted grease. This now can be achieved with all standard components within a complicated mold assembly, not just with the ejector pins. More complex components – such as 2-stage ejection and latch locks, guide pins, ejector pins, sleeves and blades to lifters and side actions – are being produced as standard off -the-shelf components with DLC coating. The costs for DLC-coated standard vs. non-coated standard items can be justifi ed with the extended life of most tooling.
Brenda Clark has been working for over 35 years in the plastics industry in engineering, mold design and sales. HASCO’s specialties include areas of standard mold bases – metric and inch, mold base components, technical specialty components for special mold base operations, hot runner systems, customer service and application reviews for new and old molds. HASCO was founded in 1924 in Lüdenscheid, Germany, and today is the international leading supplier of modular standardized components and accessories. Its range takes in more than 100,000 products, providing customized and cost-efficient solutions for tool and moldmaking, as well as for the plastics processing industry. For more information, email bclark@hasco.com or visit www.hasco.com.