By Christopher Spada, LSG & SFG Technical Sales/Product Management, Jergens
In the realm of lifting, the number-one priority isn’t just getting something off the ground and relocated – it’s worker safety. That widely is known. No company wants to put its employees’ safety in jeopardy. Injury on a personal level is regrettable and can be tragic, and on a business level, very costly in terms of time, money, fines, litigation and productivity. For these reasons, there are safety standards that call out specifications that must be met long before anything is hooked up to be moved. One such comprehensive standard is B30.26, as set forth by the American Society of Mechanical Engineers (ASME).
According to ASME,“B30.26 applies to the construction, installation, operation, inspection and maintenance of detachable rigging hardware used for load-handling activities in conjunction with equipment described in other volumes of the B30 Standard. This hardware includes shackles, links, rings, swivels, turnbuckles, eyebolts, hoist rings, wire rope clips, wedge sockets, rigging blocks and load indication devices.” 1
There are many aspects to this standard that cover the equipment specifications, procedures, training and personnel. Anyone reading this and involved with lifting as part of their job function no doubt has a full copy of the standard and is on the way to compliance, if not already there.
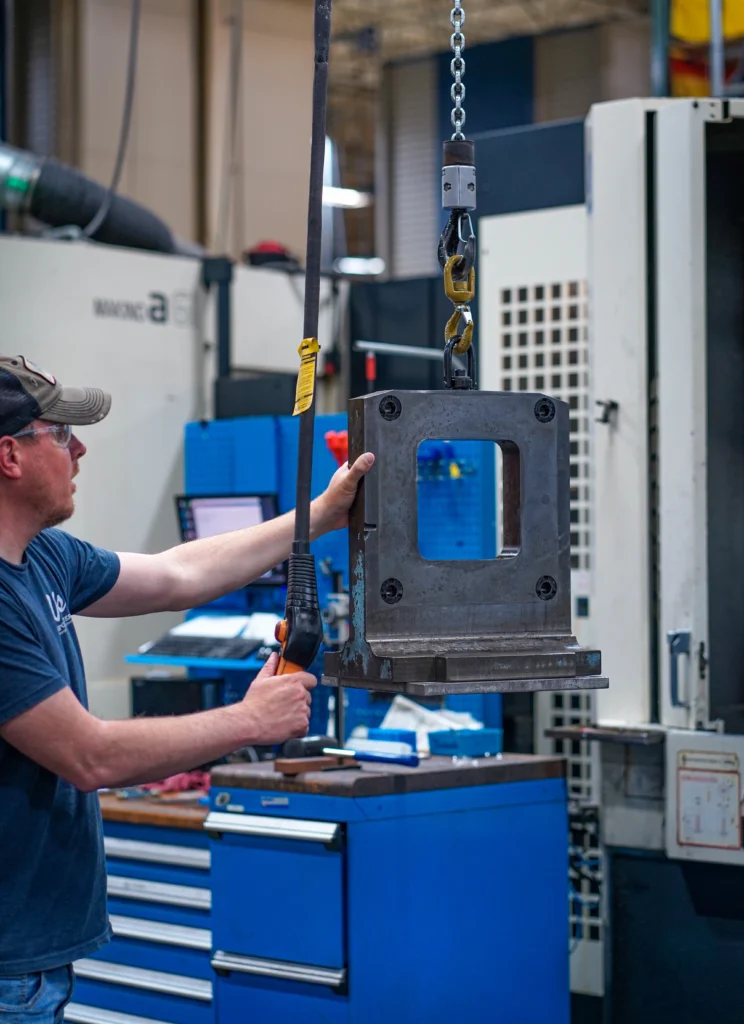
When it comes to equipment, there are several common choices for lifting, including turnbuckles, eye nuts, eye bolts and hoist rings, all under the category of “Adjustable Hardware.” That term implies moving parts or items that can be configured which also means human interaction. Both are potential areas where things can begin to go wrong. The standard describes the proper procedure for selection, use and maintenance of these items and, when followed, ensures secure and safe practices for the full range of applications. Yet, despite the detailed information, there are many instances where companies unknowingly are not in compliance, and thereby put worker safety at risk.
Following the standard is best practice and will help with compliance, security and safe lifting. Here are five things to emphasize that will help avoid potential gaps in a company’s operation that can become larger problems as time passes.
1. Conduct Inspections
These are called out in the standard but can be overlooked. There are three legs for proper inspection, and they’re designed to make sure personnel are thorough. The first is an initial inspection – when the item is received to verify that it complies. The second is frequent – this is an interval that occurs before use to ensure that there has been no damage and that the device can handle the load. The third is periodic – along the lines of once per year at a minimum, depending on severity of use. Together, the inspection phases form a process that visually and physically ensures proper function.
2. Keep Written Records
Although the standard does not call for written records, it is recommended that a company keep them. Recordkeeping serves to accomplish three things: It establishes performance tracking, makes it easy to stay on pace with all maintenance intervals and provides the backup needed for safety and compliance reviews, such as those by OSHA, as it asks for written records during inspections.
3. Maximize Load Ratings
When it comes to specifying lifting products to the application, make sure employees have more than enough in their gear to safely lift heavy loads. That means going beyond just matching up weight specifications. Choose a lifting products manufacturer with a proven track record and application knowledge and that surpasses load ratings. Note that overseas-rated load ratings frequently are only 4:1, whereas in the United States, a 5:1 load rating is a requirement called out in the ASME specifications. For example, a 10,000 lbs load test must hold to destruction at 50,000 lbs, at a minimum. Getting to these high-level results requires certified materials and strict design parameters.
4. Engineer the Lift
Knowledgeable and trained lifting engineers understand critical issues for safe and reliable lifting, and they know to rig to the load. After the load weight has been identified, it is important to choose the appropriate lifting product. For straight vertical lifts, conventional eyebolts are a first choice. Multipoint picks (lifts) involve a share of load that depends on overall weight, the center of gravity and the sling angle.
When a sling angle is used, swiveling and pivoting hoist rings are needed for clearance and proper load distribution. Keep in mind that the applied load increases along with the added sling angle. Manufacturers offer tables and guidance to support appropriate load and lifting procedures (See Figure 1). Other criteria – such as lifting hole size, depth and location – are critical to address. Of those, thread depth often is not properly addressed. A couple of rules of thumb: The minimums should be 1½ times the bolt diameter for steel and two times the bolt diameter for aluminum.
5.Don’t Take Shortcuts
Lastly, use all lifting products in the manner they are intended. Have a lift plan and do not use homemade remedies, such as shop-welded nuts and washers. Also do not use nuts, spacers and washers that are not part of the original assembly. ASME requires that all lifting products be durably marked, showing the manufacturer’s name or trademark, the rated load capacity and the torque value. Replacement hardware must be per the exact manufacturer. There are many do’s to follow and don’ts to avoid, from proper torque to avoiding shock loads. Consult the standard and lifting solutions provider for full and proper procedures. As the adage goes, a chain only is as strong as its weakest link.
Chris Spada has been with Jergens since 2000, beginning his current role as product manager for LSG/SFG in 2014. For Spada, it’s about educating on what Jergens offers and on how to use it properly. But the most rewarding part is helping customers achieve what they need to do and to do it successfully and safely. Jergens, Inc. is a global manufacturer of lifting, fastening and CNC workholding products. With its many lifting solutions, Jergens ensures 5:1 load rating and supports customers with experience and engineering to maximize load safety while meeting strict requirements. The company maintains many important certifications and is committed to helping customers achieve leaner, more profitable manufacturing and continues to add products and engineered solutions for an integrated approach to “manufacturing efficiency.”
References
- The American Society of Mechanical Engineers. https://www.asme.org/codes-standards/find-codes-standards/b30-26-rigging-hardware