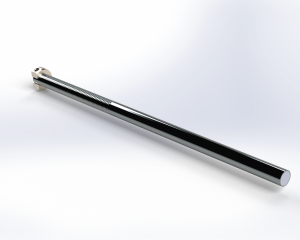
Next Chapter Manufacturing, Grand Rapids, Michigan, recently debuted its newest technology – InnoVent Technology. InnoVent aims to solve the issue of gas traps that injection molders face. When molten resins are injected into the mold cavity, air can easily become trapped inside the mold. The trapped air can then become compressed. This is associated with a sharp rise in temperature that damages the material and can damage the mold itself. Gas traps frequently cause cosmetic defects to the product, and functional or mechanical defects also can occur. As a result, the defective product is scrapped.
Next Chapter’s InnoVent Pins allow injection molders to vent the part, not the line. The pins are capable of venting 10 to 15 times more gas than traditional ejector pins without clogging and without requiring excessive maintenance and quality control investments. InnoVent Technology is hot swappable with standard ejector pins and making the switch to InnoVent does not require any mold modifications. Even with abrasive resins, InnoVent Pins inflict less wear and tear on the mold. For a mold that ordinarily requires 100 standard pins can be completed with two to three InnoVent Pins. For more information, visit www.nxcmfg.com.